New publications
Microwave pyrolysis - a new technology for waste recycling
Last reviewed: 02.07.2025
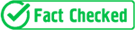
All iLive content is medically reviewed or fact checked to ensure as much factual accuracy as possible.
We have strict sourcing guidelines and only link to reputable media sites, academic research institutions and, whenever possible, medically peer reviewed studies. Note that the numbers in parentheses ([1], [2], etc.) are clickable links to these studies.
If you feel that any of our content is inaccurate, out-of-date, or otherwise questionable, please select it and press Ctrl + Enter.
Plastic-aluminum laminate packaging - most people will say that they have not heard of such packaging, but almost everyone has encountered it in their daily life. Such packaging has long been used to make toothpaste tubes, but in recent years they have been actively used for drinks, food products or pet food.
Currently, this type of packaging is in third place, after aluminum and plastic bottles. The only thing that distinguishes laminate packaging from other types of packaging is the absence of a sign indicating the possibility of recycling.
But for manufacturers, it is plastic-aluminum laminate packaging that is extremely attractive, since its production requires little energy, it is lightweight, which reduces transportation costs, and this type of packaging provides good protection from light and the negative impact of external factors.
Every year the popularity of this type of packaging increases by 10-15%, since there are no real reasons to abandon this type of packaging.
It is worth noting that in the UK, over 170,000 tonnes of laminate are used each year to produce such packaging, with 17,000 tonnes of aluminium going underground.
The idea of recycling such packaging came from Dr. Carlos Ludlow-Palafox from the University of Cambridge. Back in 1997, the professor heard a story about how a bacon roll was kept in a microwave oven for too long, which turned the food into red coals. In the microwave oven, a pyrolysis process occurred, which was provoked by microwave radiation. Under the influence of high temperatures, organic materials decomposed. During the pyrolysis process, the metal that is part of the material was released.
Carlos' work began with placing granulated carbon and a piece of laminate packaging in a regular microwave oven, after which he replaced the air inside the oven with nitrogen. Then he turned on the oven at full power (1.2 kW), after about 2 minutes, after the temperature inside the oven reached 600 C0, the laminate began to separate into oils, gaseous carbons and aluminum flakes.
Now, 15 years later, the researchers have decided to test the method at a plant in Lutten, UK. The plant uses a principle similar to that of a conventional microwave oven, with the only difference being that the plant's oven has a power of 150 kW.
The entire process, which converts packaging into aluminum and hydrocarbons, takes three minutes and does not release any toxic emissions into the atmosphere. The aluminum obtained in this way can be used for further remelting, and the hydrocarbons for fuel production.
This waste recycling plant is partly sponsored by large food giants, and is already fully prepared to begin work on recycling laminate packaging. According to estimates, the plant will be able to recycle more than 2 thousand tons of packaging annually, while being completely self-sufficient, generating enough energy. In addition, an agreement has already been concluded with manufacturers of plastic-aluminum laminate packaging for the recycling of industrial waste, while the cost of sending it to the recycling plant for manufacturers will be less than the cost of sending it to a landfill.
The researchers' work does not stop there. Carlos' group is already testing various materials by subjecting them to microwave pyrolysis.